Analysis Of The Reasons For Low Outlet Pressure Of Centrifuga
TIME:2024-08-20 Author:admin Views:
Analysis Of The Reasons For Low Outlet Pressure Of Centrifugal Pump
Due to the wiring, the direction of the motor will be opposite to the actual required direction of the centrifugal pump. Therefore, when starting, you should first observe the direction of the pump. If the direction is reversed, you should swap any two wires on the motor terminals.
The working point is offset to high flow and low head
Under normal circumstances, chemical centrifugal pumps have a continuous downward performance curve, and the flow rate gradually increases with the decrease of head. During the operation process, due to some reason, the pump back pressure is reduced, and the pump working point passively shifts to the low head and high flow point along the device curve, which will cause the head to decrease. In fact, this is caused by external factors such as changes in the device, and has no special relationship with the pump itself. At this time, as long as the pump back pressure is increased, such as closing a little outlet valve, the problem can be solved.
Speed reduction
The important factors affecting the head of the chemical centrifugal pump are the outer diameter of the impeller and the speed of the pump. When other conditions remain unchanged, the head of the pump is directly proportional to the square of the speed. It can be seen that the speed has a great influence on the head. Sometimes, due to some external reasons, the speed of the centrifugal pump is reduced, which will reduce the pump head accordingly. At this time, the pump speed should be checked. If the speed is indeed insufficient, the cause should be checked and solved reasonably.
Cavitation at the inlet
If the suction pressure of the pump is too low, lower than the saturated vapor pressure of the pumped medium, cavitation will occur. At this time, check whether the inlet pipeline system is blocked or the inlet valve opening is too small, or increase the liquid level of the suction pool.
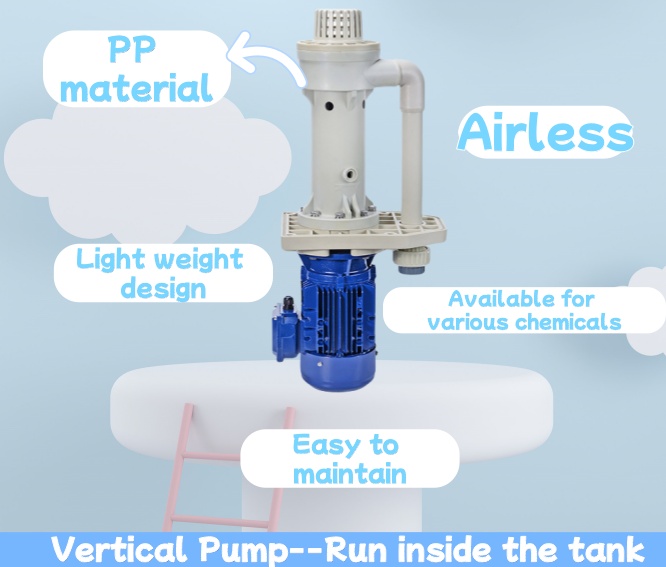
Internal leakage
When the gap between the rotating part and the stationary part in the chemical pump exceeds the design range, it will cause internal leakage, which is reflected in the decrease of the discharge pressure of the pump, such as the gap between the impeller ring and the interstage gap of the multistage pump. At this time, the corresponding disassembly and inspection should be carried out, and the parts that cause the gap to be too large should be repaired or replaced.
Impeller flow channel blockage
If the impeller part of the flow channel is blocked, it will affect the work of the impeller and cause the outlet pressure to drop. Therefore, it is necessary to disassemble the pump to check and remove foreign matter. To prevent this problem from happening again, a filter device can be added before the pump inlet if necessary.